Sistemele de management – organizare, reducere a costurilor şi disponibilizări
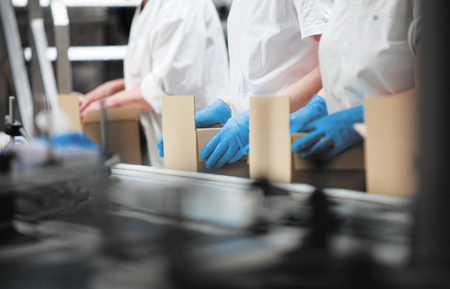
Trecerea timpului ne-a arătat că nu sunt mulţi producători care au rămas profitabili în recesiune. Printre puţinii care au reuşit această performanţă se numără şi companiile care au folosit un sistem de management performant pentru a deveni mai eficiente din punctul de vedere al costurilor. Lean Management, de exemplu, reprezintă un corp de bune practici aplicabile în domeniul optimizării operaţionale şi a dezvoltării de produs, care pune bazele pentru ca firmele să treacă de la un stadiu de dezvoltare bazat pe exploatare intensivă a forţei de muncă ieftine, la creşterea valorii adăugate prin inovaţie şi organizare superioară. Aceasta presupune efectuarea fiecărei acţiuni din companie într-un flux neîntrerupt şi producerea exclusivă a lucrurilor pe care le cer clienţii, prin tăierea fără milă a miliarde de lei, dolari sau euro din inventar. Un mare avantaj, după cum spun patronii micilor firme, este manipularea unei cantităţi mai mici de materiale, mai puţină mişcare şi mai puţine deşeuri. Pe termen scurt, producătorii ajung să reducă stocurile, dar şi forţa de muncă. Experţii sunt de părere că, implementând acest sistem de management, recuperarea ar putea fi încetinită sau amânată. Desigur, cu toţii ne amintim de revoltele angajaţilor Dacia care au fost trimişi în şomaj tehnic de nenumărate ori în ultima perioadă, deoarece compania nu avea niciun motiv să producă mai multe maşini decât cerea piaţa. Acesta poate fi, desigur, un caz fericit, deoarece vorbim despre şomaj temporar şi nu despre disponibilizări.
În unele industrii însă s-a luat decizia renunţării la unele locuri de muncă, deoarece producătorii au decis să utilizeze mai puţini angajaţi, pentru o eficientizare a costurilor, corelată cu folosirea noilor tehnologii. Cu alte cuvinte, investiţiile în aparatură au fost considerate mai eficiente, pe termen lung, decât investiţiile în oameni. Acesta poate fi unul dintre motivele pentru care Lean Managementul a fost considerat de unii specialişti în resurse umane un factor negativ pentru piaţa locurilor de muncă.
Adevărul este, ca de fiecare dată, undeva la mijloc. Şi, în cazul în care companiile nu adoptă un management de tăiere a costurilor, riscă să ajungă la faliment, moment în care toţi angajaţii ar rămâne fără joburi.
De aceea se consideră că, adoptând un sistem performant de management, manevrele sunt menite să ajute companiile să menţină profiturile şi să angajeze, în cele din urmă, salariaţi. Aceste măsuri de reducere a costurilor au fost luate în întreaga lume, ca un răspuns la presiunile de cost aduse de globalizare, în ideea de a produce mai ieftin şi mai eficient. Cu alte cuvinte, un management de supravieţuire.
Lean Management este în prezent una dintre cele mai cunoscute metode de management pentru companiile de producţie (de aceea este cunoscut mai ales ca Lean Manufacturing). Metoda Lean se utilizează în corelare cu instrumentul calităţii, denumit „6 sigma”, care are la bază sistemul de producţie Toyota. În compania Toyota acest sistem a fost realizat la sfârşitul anilor `80, ca o modalitate de a reduce cantitatea de deşeuri şi pentru eliminarea paşilor de producţie. În timp, tot mai multe companii au adoptat practicile Toyota. Sistemul a fost adaptat în 1995 pentru companiile vestice. Numărul celor care au implementat Lean a crescut în mod substanţial abia în timpul crizei economice. În Statele Unite ale Americii, 61% dintre producătorii au declarat că au adoptat Lean Management sau intenţionează să facă acest lucru în acest an.
Aplicarea Lean Manufacturing furnizează rezultate bune, fără a fi nevoie de sisteme complicate, deci, este o metodă adecvată şi pentru IMM-urile cu resurse limitate.
Lean Manufacturing înseamnă celule sau linii de asamblare flexibile, munci mai complexe, muncitori înalt calificaţi, produse bine făcute, o varietate mult mai mare de părţi interschimbabile, obligatoriu o calitate excelentă, costuri reduse prin îmbunătăţirea procesului de producţie, pieţe internaţionale şi competiţie mondială. Lean Manufacturing sau producţia la costuri minime reprezintă o filosofie de producţie ce determină reducerea duratei de la comanda clientului până la expedierea produsului, prin eliminarea pierderilor.
Bazat pe sistemul de producţie Toyota, Lean a evoluat dincolo de rădăcinile sale, astfel că livrează „reţeta succesului” şi în alte sectoare decât cel de producţie. „Acum cinci ani, unii oameni au susţinut că instrumentele Lean nu au fost adecvate pentru sectorul public sau de îngrijire a sănătăţii, dar acum şi-au schimbat opinia”, explică Lee Young, Senior Manager Deloitte, responsabilă pentru aplicarea Lean în domeniul sănătăţii. Astfel sectorul public şi organizaţiile de îngrijire a sănătăţii din întreaga Americă de Nord au adoptat sistemul Lean Management şi şi-au îmbunătăţit modul de organizare, mai ales prin orientarea pe pacient, pe capacitatea de a crea servicii de calitate la costuri reduse.
O companie care doreşte să aplice Lean Management trebuie să parcurgă mai multe etape. Mai exact, pentru a implementa Lean trebuie realizate: diagnosticul situaţiei iniţiale, stabilirea acţiunilor de întreprins, aplicarea şi măsurarea rezultatelor, analiza situaţiei îmbunătăţite, şi nu numai.
Trebuie ştiut însă că reducerea costurilor dintr-o organizaţie se poate face prin mai multe metode. Totul începe, de fapt, de la fiecare angajat în parte. Un studiu realizat în urmă cu ceva timp în Statele Unite arată că peste 50% dintre manageri consideră ordinea de pe biroul angajaţilor ca un plus la promovarea acestora şi că 51% făceau o corelare între curăţenia de pe birou şi productivitate. Dar, în acelaşi timp, 49% dintre aceşti manageri se considerau profesionişti şi relaxaţi dacă aveau pe mese câteva teancuri ordonate de documente, iar 31% chiar acceptau un haos organizat pe birourile lor. Cu alte cuvinte, fiecare manager poate fi considerat „vinovat” de sistemul de management pe care îl adoptă în companie.
Ce sistem de management te ajută să rezişti de 50 de ani pe piaţa medicamentelor din România?
Poate vă întrebaţi cum mărci renumite, precum Gerovital H3, Antinevralgic, Algocalmin, Extraveral, Distonocalm sunt şi astăzi cunoscute de toţi românii. Compania Zentiva, care aniversează anul acesta 50 de ani de activitate, fiind de jumătate de secol producătorul numărul unu de medicamente din România, poziţie de lider pe care şi-a păstrat-o până astăzi, a implementat în ultimii ani diverse sisteme de management. De anul trecut Zentiva – o companie Sanofi – a integrat şi sistemul de management Lean.
„După preluarea companiei Zentiva de către grupul Sanofi, Divizia Industrială din România – care înseamnă Fabrica de Medicamente – şi-a reluat curba de dezvoltare pe care încercăm să o susţinem cu ajutorul unui management atent al performanţei”, spune Margareta Tănase, Director Operaţiuni Industriale Zentiva.
Managementul performanţei nu înseamnă însă numai o serie de reglementări de care ştiu şi ţin seama doar oamenii din conducerea companiei, ci reguli care se aplică angajaţilor pentru a obţine rezultate mai bune, pentru satisfacerea nevoilor clienţilor şi, nu în ultimul rând, pentru reducerea costurilor.
Astfel, în perioada 2004-2007 a fost implementat un Sistem de Management Integrat Calitate-Mediu-Sănătate şi Securitate Ocupaţională (ISO 9001 – ISO 14001 – OHSAS 18001). De asemenea, o atenţie deosebită a fost acordată aplicării metodelor specifice de management de proiecte.
În ceea ce priveşte managementul prin obiective, la Zentiva România performanţa angajaţilor se măsoară printr-un sistem complex care evaluează atât performanţa colectivă, cât şi pe cea individuală, respectiv rezultatele şi modul în care au fost obţinute. Un element important este şi cel de recunoaştere, deoarece există un sistem prin care angajaţii model sunt apreciaţi pentru contribuţia lor. „Pentru componenta colectivă am stabilit o serie de indicatori de performanţă şi toate rezultatele sunt comunicate transparent pe parcursul anului către angajaţi”, adaugă Angela Posdărăscu, HRS&HSE Manager Divizia Operaţiuni Industriale Zentiva. În ceea ce priveşte performanţa industrială, aceasta este urmărită prin instrumente specifice, cum ar fi dashboard-ul de KPI, corelat cu performanţa financiară care asigură atribute de competitivitate.
Primul pas, definirea strategiei
Un sistem de management al performanţei angajaţilor, altul pentru evaluarea performanţei industriale, altul pentru calitate, mediu, şi aşa mai departe. Cum se pot integra toate aceste mici puzzle-uri care constituie întregul sistem de management al companiei într-unul singur?
Ca şi alte mari companii din România, dar şi din lume, Zentiva România a început să implementeze, la începutul anului trecut, sistemul de management Lean. „Cheia managementului Lean este să îţi propui un obiectiv ambiţios, cu 50% mai performant decât ceea ce se întâmplă în mod curent, iar rezultatele care se observă cel mai uşor vin din modul de organizare şi alocare de resurse”, spune Margareta Tănase.
Primul pas în implementarea principiilor Lean în companie a fost definirea strategiei, care cuprinde viziunea pentru următorii cinci ani. Primele acţiuni concrete au fost workshop-urile Lab&Land în producţie pe metodele SMED (o metodă rapidă şi eficientă de a face schimbări pe liniile de fabricaţie) şi Management Vizual. De asemenea, din luna octombrie există la Zentiva un nou departament care a preluat activitatea dezvoltată anterior de Performanţa Industrială, combinată cu activitatea de îmbunătăţire continuă, şi care a dezvoltat o reţea de campioni Lean. Aceştia asigură susţinerea sistemului de management.
„Orice angajat poate să propună îmbunătăţiri simple sau inovaţii care necesită alocări de resurse”, explică Angela Posdărăscu.
Succesul unui astfel de demers este cu atât mai sigur cu cât în fabrica noastră lucrează oameni cu peste 20 de ani de experienţă. Expertiza lor este foarte importantă, aduce valoare, garantează că schimbarea este benefică, nu atinge nivelul ridicat de calitate decât în sens pozitiv.
„Suntem în plină implementare a filosofiei Lean, iar primele rezultate au venit după organizarea workshop-urilor în zona de ambalare, unde am redus la jumătate timpul dedicat schimbărilor de produs şi am devenit o referinţă în cadrul grupului”, spune Margareta Tănase. Mai exact, după această perioadă de început, managementul Zentiva a reuşit să se adapteze rapid la schimbare, este mai pregătit să facă faţă provocărilor de pe piaţă, face doar ceea ce este necesar, cu oamenii care produc valoarea.
„Unul dintre obiectivele noastre este să asimilăm în cultura noastră organizaţională elementele Lean, iar aceasta a însemnat să ne concentrăm pe a dărâma paradigma care spunea că managementul trebuie să propună liniile directoare de acţiune, să rezolve problemele şi să aducă îmbunătăţiri în producţie”, adaugă Margareta Tănase. De exemplu, operatorii care lucrează în fiecare zi în producţie sunt cei care cunosc mult mai bine aspectele care ar putea fi îmbunătăţite, şi de la ei porneşte acum schimbarea. „Responsabilizarea colegilor a fost naturală, a venit din participarea în cadrul workshop-urilor, a monitorizărilor ulterioare şi a fost motivată de rezultatele imediate, care te determină să participi activ” explică Angela Posdărăscu cum s-au mobilizat angajaţii.
Compania a decis să investească în pregătirea angajaţilor, pentru a se asigura că s-au înţeles principiile şi direcţiile de dezvoltare, implicarea tuturor în schimbare fiind principalul factor de succes. Astfel, în luna septembrie au desfăşurat un program maraton de training, Fabrica de Valori, la care au participat 200 de angajaţi. Practic, a fost o săptămână educaţională care a gravitat în jurul culturii Lean. „O zi întreagă a fost dedicată rezolvării de probleme şi generării de idei. Am prezentat metodologia şi au fost discutate problemele reale cu care ne confruntăm în activitatea zilnică.”
În cifre, Fabrica de Valori a însemnat: 5 zile de training, 19 traineri interni, manageri de departamente și specialiști, 200 de participanți, operatori din zonele de producție, analiști din laboratoarele de control al calității, operatori din depozite și personal suport, peste 7.200 de ore de training, dar, cel mai important, 300 de idei colectate în timpul workshop-urilor.
„Mereu ne propunem programe provocatoare. Sperăm că după implementarea completă a programului Lean în toată organizaţia vom gândi în sensul culturii de îmbunătăţire şi vom fi mult mai concentraţi în a veni cu idei inovatoare, care aduc valoare.”
Angela Posdărăscu –HRS&HSE Manager Divizia Operaţiuni Industriale Zentiva
„Implementarea culturii de îmbunătăţire este foarte importantă pentru noi şi toţi angajaţii noştri trebuie să vorbească aceeaşi limbă. Este o ţintă cu adevărat provocatoare ca în 2016 să avem câte 10 sugestii per angajat implementate pe an şi acesta este un nou pas în trecerea de la mentalitatea de tipul «raportarea problemei» la cea de tipul «idei de rezolvare a acesteia».”
Margareta Tănase – Director Operaţiuni Industriale Zentiva
Articol preluat din Revista Cariere de noiembrie. Pentru detalii legate de abonare, click aici